
成形設備
小ロットから大ロットまで高品質な
生産が行えるゴーシューの
鍛造の根幹となる設備です。

熱間成形ライン
2000~
4000TON
×7
4000TON
2000TON
×8
600~
1000TON
×7
1000TON
月産
610万個
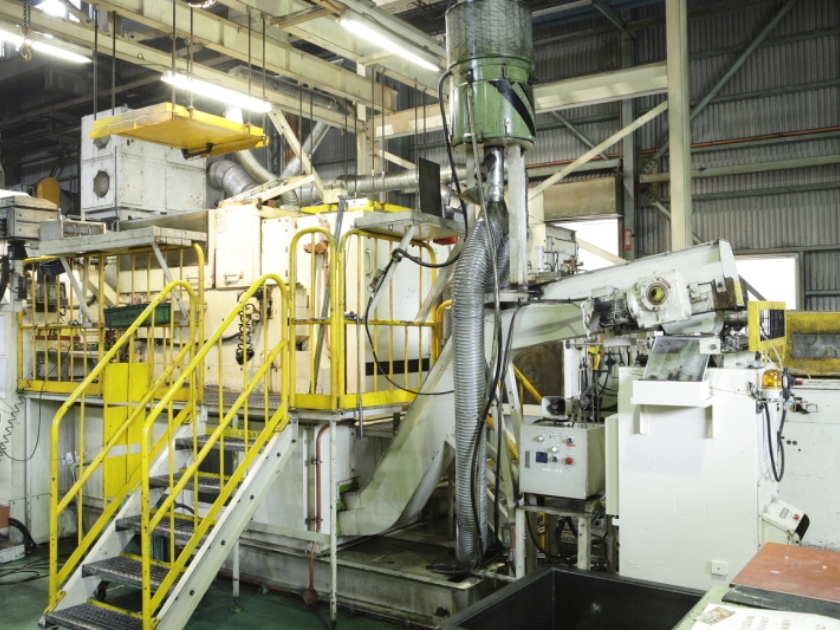
冷間成形ライン
340TON
フォーマー
ライン
×1
フォーマー
ライン
フロー
フォーミング
ライン
×3
フォーミング
ライン
月産
310万個
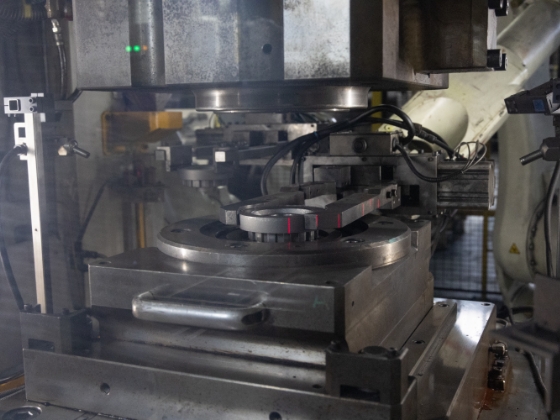
冷間サイジングライン
630~
1600TON
×7
1600TON
200~
600TON
×10
600TON
月産
205万個
熱処理設備
100%内製化を行い、
製品の機械的性質や
機械加工性等の確保と
品質保証の確立を行っています。

素材熱処理
- 連続式焼入焼戻炉
- 連続式焼ならし炉
- ベル型焼きなまし炉
月産
2,900TON
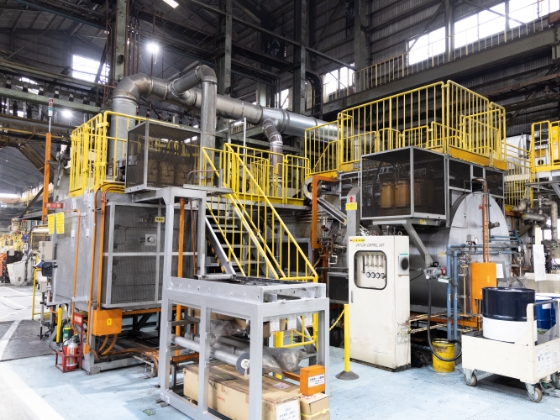
加工熱処理炉
- 完成品熱処理
- 浸炭焼入焼戻炉
- 真空焼入焼戻炉
月産
27TON
金型生産設備
独自ノウハウを
早く3次元の形状に変換することと、
成形部の精度向上・
低コスト化のため、
主要金型は内製化を行っています。

- 直彫り加工機8台
- 型彫り放電加工機13台
- ワイヤー放電加工機4台
- レーザー加工機1台
- 非接触3D測定機1台
- 3D CAD/CAM5台
技術設計設備
2Dから3Dへの一元化と、
事前に検証できるCAEシステムで、
より精度の高い
オペレーション設計を
展開致しています。

- 2D CAD Auto CAD
- 3D CAD Unigraphics
- CAE DEFORM-2D
- CAE DEFORM-3D
主要検査・試験設備
要求された製品機能を
スピーディー、かつ高精度で
評価する体制を整えています。
-
3Dスキャナー
-
3次元測定機
- 走査型電子顕微鏡(SEM)
- サーフテスト
(面粗度測定機) - 真円度測定機
- 形状投影機
- ベベルギヤ用噛合試験機
- 引張試験機
- シャルピー衝撃試験機
- ビッカース硬度計
- ロックウェル硬度計
- マイクロスコープ
生産・品質管理
製造の高効率化実現のための
重要課題は、
あらゆるロスを無くすこと。
そこには現場を観、
ニーズを先取り、
そしてスピードが要求されます。
ゴーシューは経験と実績に培われた
確かなデータ分析と評価に基づき、
ISOをベースとした
管理体制を確立。
人間とIT(情報技術)が
一体となった生産・品質管理を
実現しています。
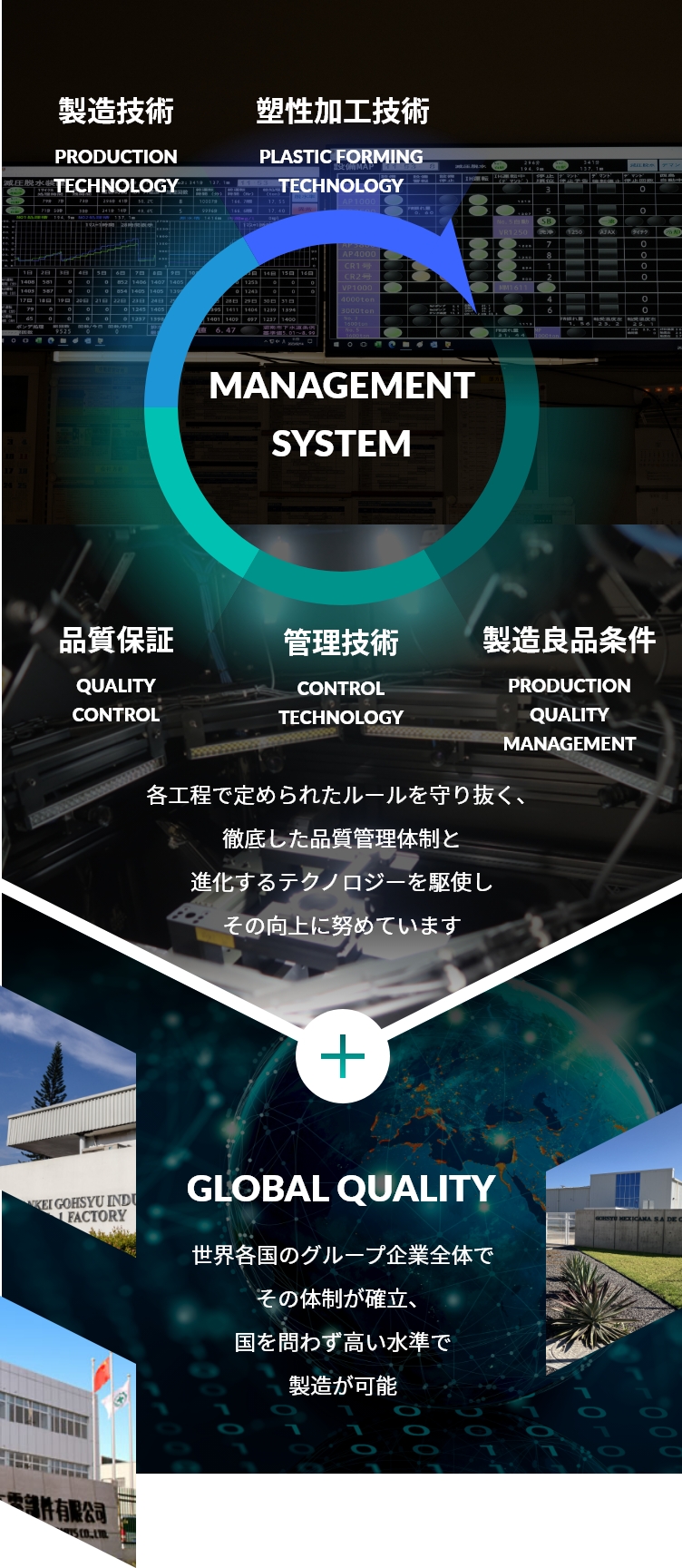
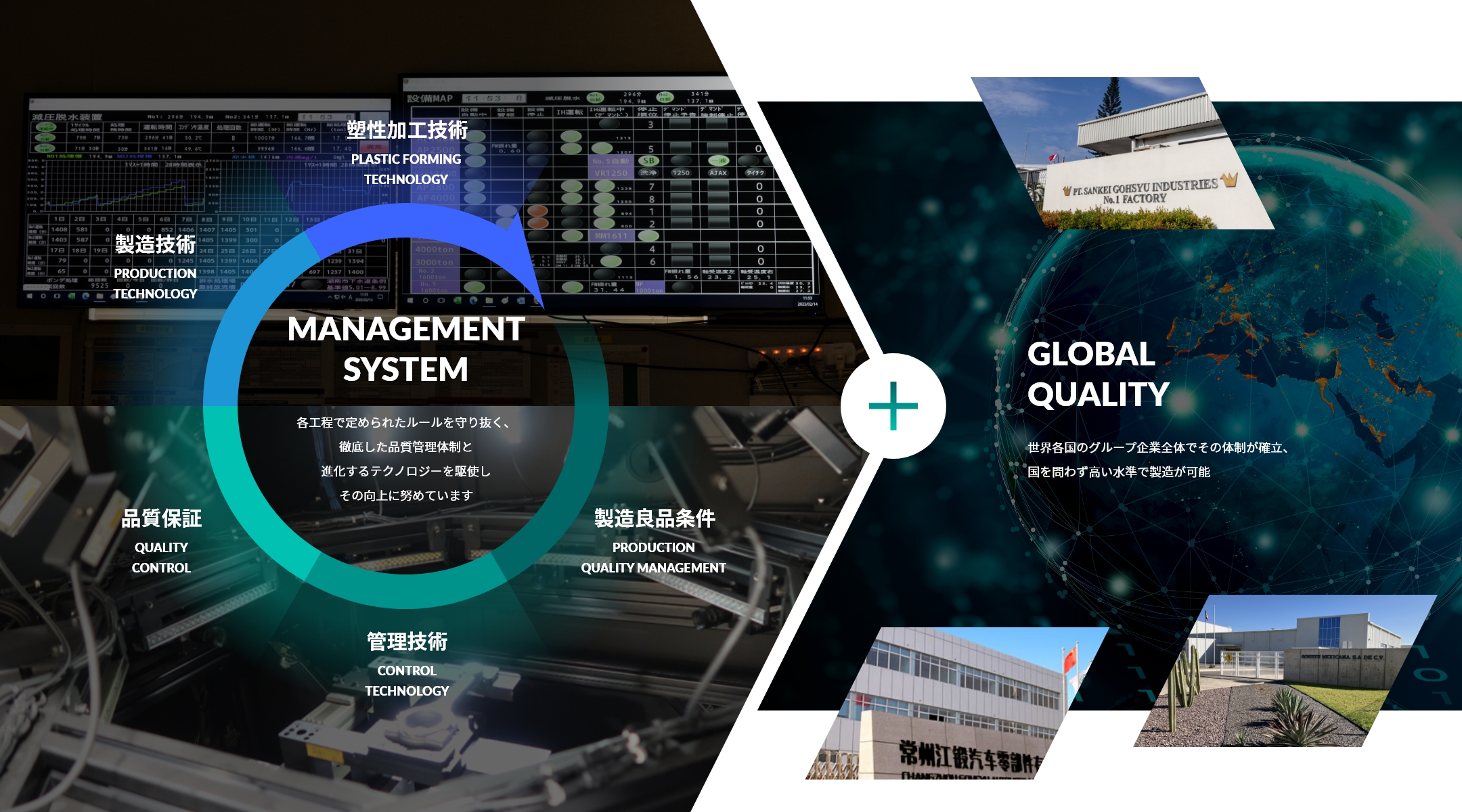
ご発注の流れ
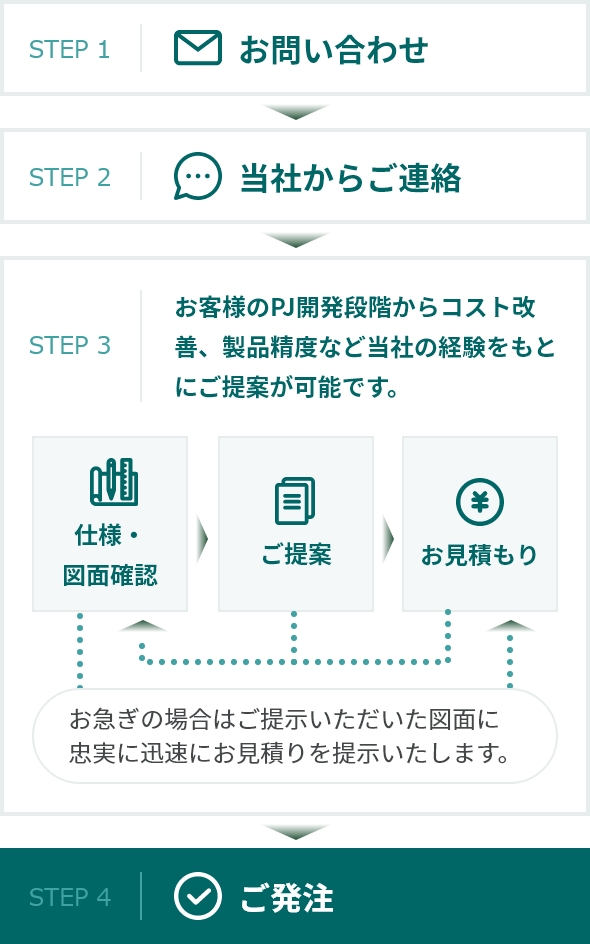
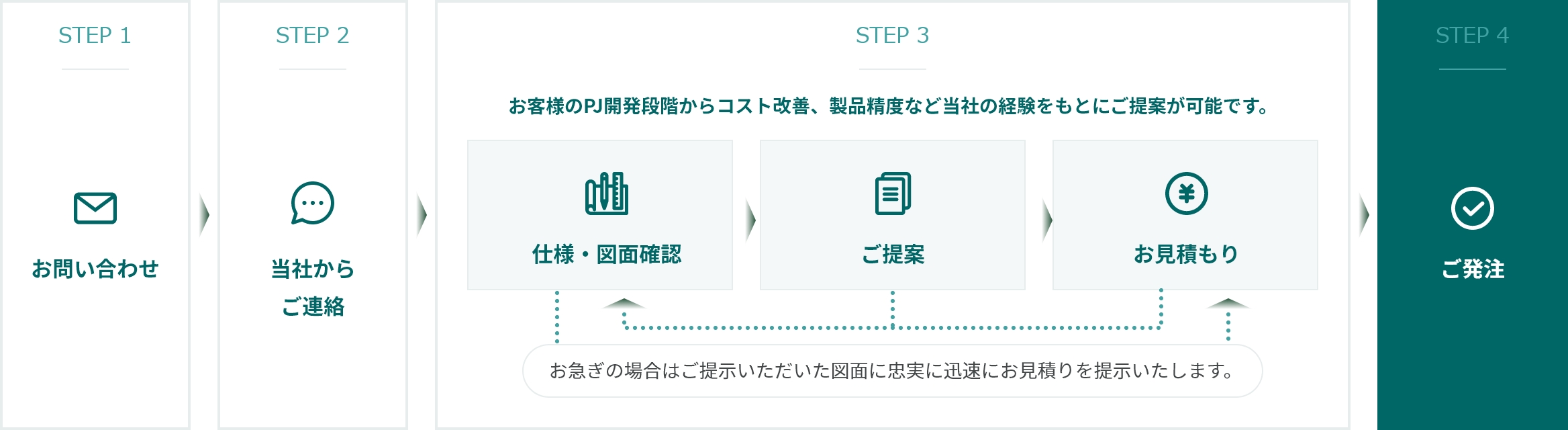

contactお問い合わせ
